Understanding Instrument Fitting Size - A Comprehensive Guide
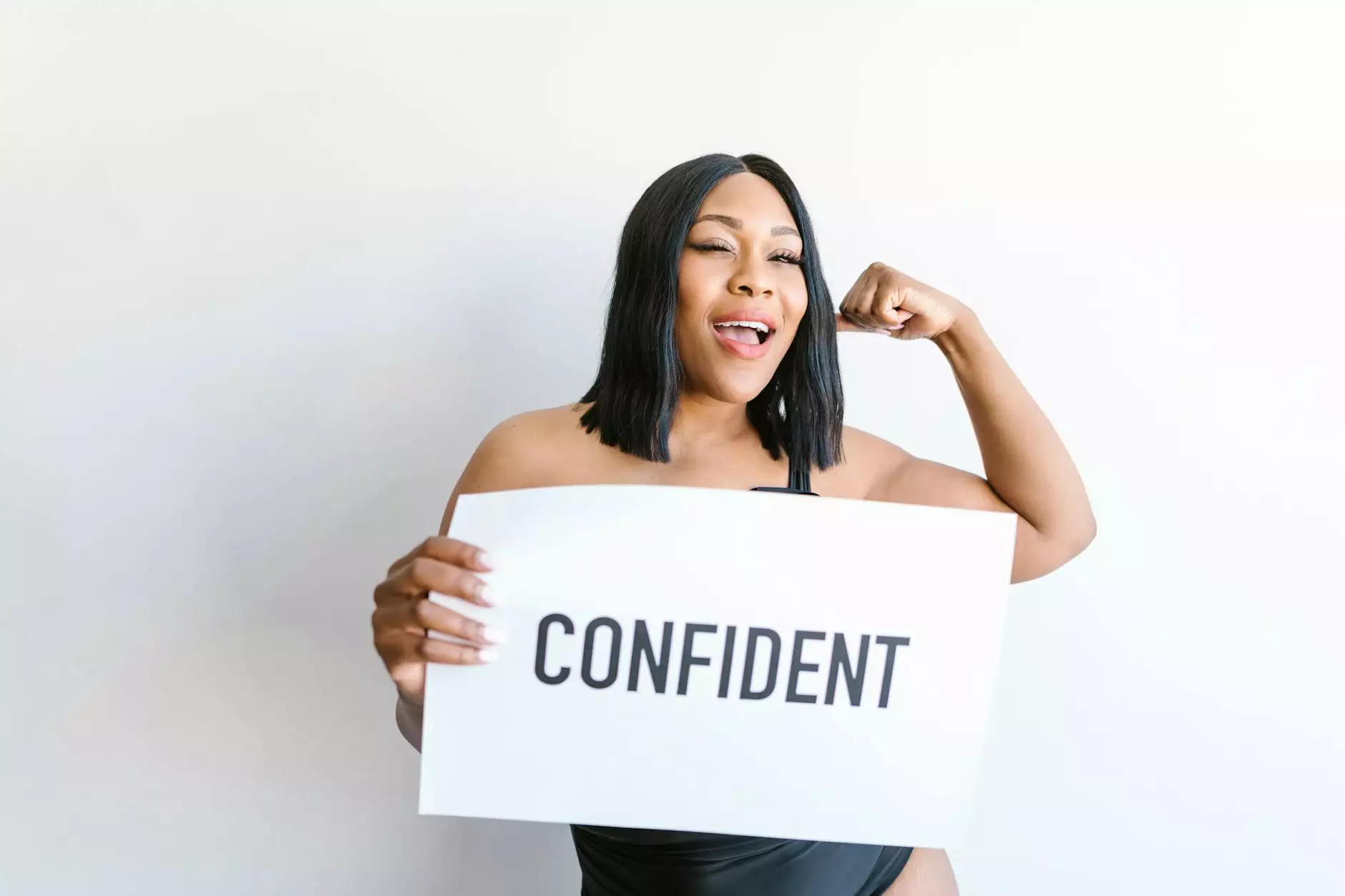
Instrument fitting size is a critical component in a variety of industrial applications, particularly in fluid and gas systems. Choosing the correct size not only ensures efficient system operation but also significantly impacts safety and performance. This article aims to provide a detailed overview of instrument fitting size, its relevance in various industries, and how to select the right fittings from trusted suppliers like Techtubes.
What Are Instrument Fittings?
Instrument fittings are specialized components that assist in connecting and controlling the flow of fluids or gases in piping systems. These fittings are essential in maintaining the integrity of the system and ensuring that they can accommodate various pressures and temperatures. The correct instrument fitting size is crucial as it affects the overall performance and reliability of the system.
The Importance of Instrument Fitting Size
The instrument fitting size is not a mere specification; it is fundamental to various aspects of piping systems:
- Flow Efficiency: The correct size ensures optimal fluid or gas flow through the system, minimizing resistance and energy loss.
- Leak Prevention: Properly sized fittings reduce the likelihood of leaks, which can lead to safety hazards and environmental concerns.
- compatibility: Different systems have varying requirements. The right size ensures compatibility with other components, such as valves and pipes.
- Maintenance Ease: Correct sizing simplifies installation and maintenance, saving time and reducing costs.
Types of Instrument Fittings
Various types of instrument fittings are available in the market, each designed for specific applications. Some common types include:
- Tube Fittings: These are used for making connections in tubing systems, providing a strong, leak-proof seal.
- Ferrule Fittings: They consist of a ferrule and a nut, offering a reliable connection for tubing.
- Forged Pipe Fittings: Made from a single piece of metal, these fittings are known for their strength and durability.
- Threaded Pipe Fittings: These fittings use threads to connect to pipes, allowing for easy assembly and disassembly.
- Flanges: Flanged fittings provide a strong, stable connection between piping systems.
- Check Valves: These prevent backflow in a system, ensuring that fluids move in one direction.
- Ball Valves: These allow for quick shut-off in flow applications.
- Needle Valves: Precision valves that allow fine adjustments in flow rate.
- Manifold Valves: Used for controlling multiple flow paths in a system.
- NPT Fittings: National Pipe Tapered fittings that provide a tight seal when threaded together.
How to Identify the Correct Instrument Fitting Size
Selecting the right instrument fitting size requires a few considerations:
1. Identify the Pipe or Tube Size
Begin by measuring the outer diameter (OD) of the pipe or tube you are working with. It is important to ensure you are measuring accurately, as even small discrepancies can lead to incorrect fitting sizes. For instance, if you are working with a standard pipe, knowing if it is a schedule 40 or schedule 80 can help you determine the correct fitting size.
2. Understand the Type of Fitting Required
Depending on your application, you may require a specific type of fitting. For instance, tube fittings require distinct measurements compared to threaded pipe fittings. Familiarize yourself with the specifications and dimensions for each type to accurately determine the appropriate size.
3. Consider Pressure and Temperature Ratings
Different materials exhibit varying performance characteristics under pressure and temperature. Ensure that the fittings you choose are rated for the conditions they will face. This consideration can help in avoiding premature failure of the components in your system.
4. Check Industry Standards
Standards such as ASTM, ANSI, and ASME dictate the sizing and dimensions for various fittings. Consult these standards to find precise sizes and ensure compliance with industry regulations. Adhering to these standards not only guarantees quality but also enhances safety.
Common Applications for Instrument Fittings
Instrument fittings are integral in numerous industries, performing vital roles in various applications:
- Oil and Gas: Used in pipelines, refineries, and storage tanks to control the flow of oil and gas.
- Chemical Processing: Instrument fittings ensure safe chemical handling and transportation in processing plants.
- Water Treatment: Utilized in systems for managing and treating water for public supplies.
- Pharmaceuticals: Instrument fittings ensure sterile and precise environments for drug manufacturing.
- Food and Beverage: Essential for maintaining hygiene and safety during food production and transportation.
Choosing the Right Supplier for Instrument Fittings
When it comes to sourcing instrument fittings, quality and reliability are paramount. Techtubes provides an extensive range of high-quality fittings catering to various industries, ensuring that your systems function properly and safely. Here are some tips on selecting the right supplier:
1. Evaluate Product Quality
Always prioritize suppliers that adhere to high-quality manufacturing standards. Check for certifications and compliance with industry regulations to ensure the fittings you purchase will perform as expected.
2. Assess Range of Products
Choose a supplier that provides a broad range of fittings to meet different applications. Having a one-stop shop can streamline your purchasing process and reduce lead times.
3. Review Customer Service
Reliable customer service is crucial. A good supplier will offer support throughout the purchasing process, including technical assistance and timely delivery.
4. Compare Pricing
While price should not be the sole factor, it is essential to compare costs across different suppliers to ensure you receive value for your money. Remember, investing in quality fittings can save you in the long run by preventing costly failures and downtime.
Conclusion
Understanding the importance of instrument fitting size is vital for anyone working in industries reliant on fluid and gas systems. By ensuring that you select the correct size and type of fitting, you contribute significantly to the safety and efficiency of your operations. With suppliers like Techtubes, you can access a variety of quality fittings and the expertise needed to make informed decisions. Always prioritize quality and compliance, and invest in the right fittings to optimize your systems.