Understanding the Benefits of **Injection Mold Manufacturing** in China
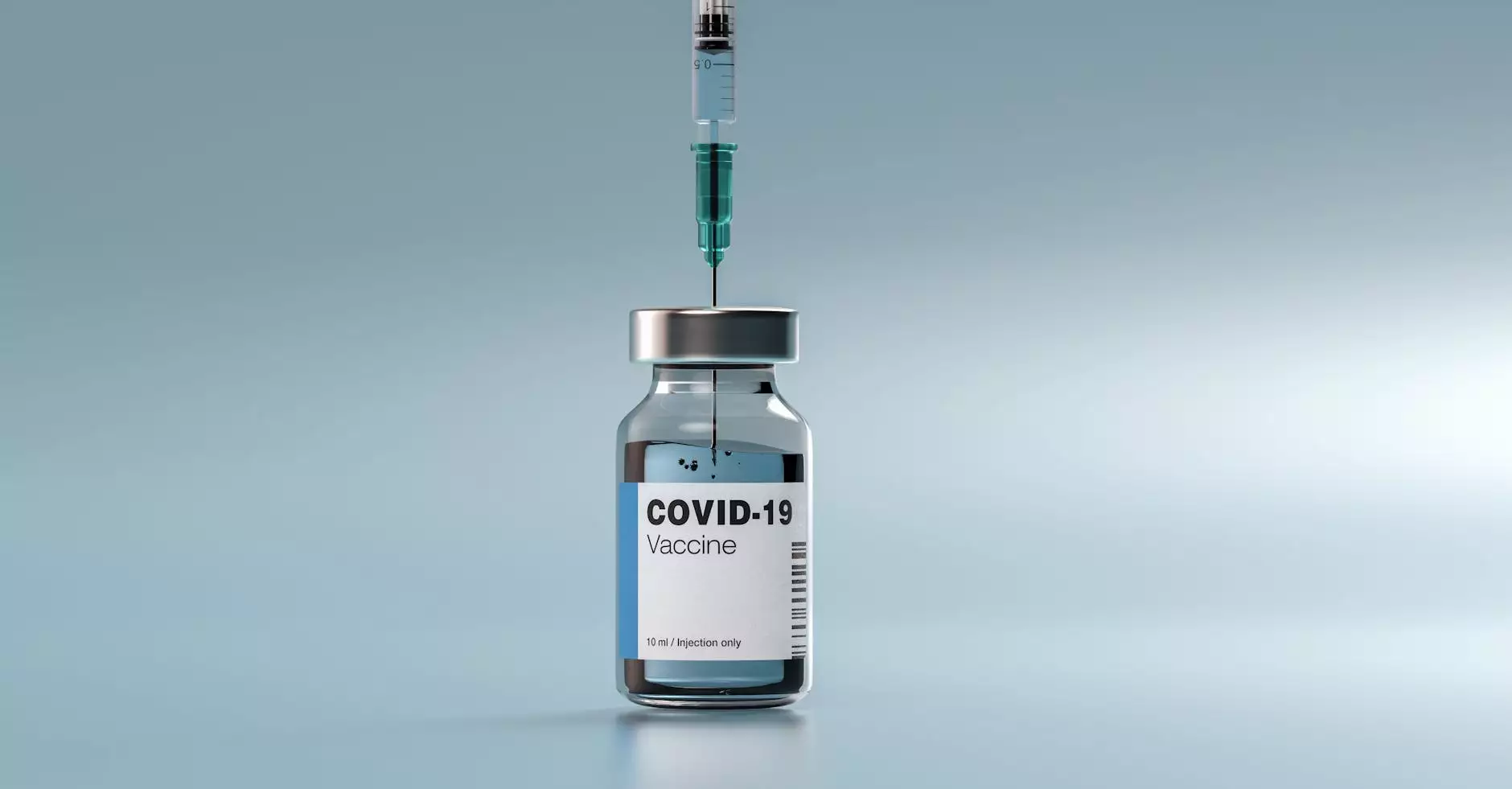
In today's global market, businesses continuously seek innovative ways to enhance their production processes while maintaining cost-efficiency. Injection mold manufacturing in China has emerged as a leading solution for companies looking to streamline their operations and produce high-quality products. This article dives deep into the advantages, processes, and future prospects of using injection molding techniques in China, especially for the metal fabrication industry.
What is Injection Molding?
Injection molding is a manufacturing process used to produce parts by injecting molten material into a mold. It is a highly efficient method for producing high volumes of complex and precise parts. Common materials used include various types of plastics, metals, and even ceramics. The process enables manufacturers to achieve consistent quality, reduce waste, and improve production speed.
Why China for Injection Mold Manufacturing?
China has positioned itself at the forefront of injection mold manufacturing for several compelling reasons:
- Cost Efficiency: The labor costs in China are significantly lower than in many Western countries, making it an attractive option for mass production.
- Advanced Technology: Chinese manufacturers have adopted cutting-edge technologies and machinery, ensuring high precision and quality in their products.
- Skilled Workforce: China boasts a large pool of skilled engineers and technicians who specialize in injection molding and metal fabrication.
- Rapid Production: The ability to produce high volumes of products quickly is another vital advantage. China's well-established supply chain allows manufacturers to minimize lead times.
The Advantages of Injection Mold Manufacturing in China
1. High Quality and Consistency
One of the primary benefits of injection mold china is the high-quality output. The precision of injection molding allows manufacturers to produce parts that meet rigid specifications consistently. This consistency is crucial for companies that require parts that fit together perfectly.
2. Cost-Effectiveness
Manufacturers can reduce costs significantly through the economies of scale that injection molding offers. With lower labor costs coupled with efficient production processes, companies can expect to see considerable savings on both their production budget and end product pricing.
3. Design Flexibility
Injection molding provides a remarkable level of design flexibility. Manufacturers can produce a wide variety of shapes and sizes with intricate designs that would be difficult or impossible to achieve with other manufacturing methods. This adaptability allows companies to innovate rapidly without the constraints usually associated with traditional fabrication methods.
4. Reduced Waste and Environmental Impact
The injection molding process allows for minimal waste generation. Excess material can often be reused, making this a more environmentally friendly option compared to other manufacturing processes. Moreover, manufacturers are increasingly adopting sustainable practices to minimize their carbon footprint, aligning with global efforts to protect the environment.
5. Quick Prototyping and Production
In the fast-paced market, the ability to develop prototypes rapidly is crucial. Injection molding allows for quick changes and adjustments in design, which accelerates the prototyping phase. This agility ensures that products can reach the market faster, giving businesses a competitive edge.
The Injection Molding Process Explained
The production process for injection molding consists of several key steps that are essential for achieving high-quality results:
- Design: The process begins with designing the part and creating a mold that outlines the geometry of the desired product.
- Mold Making: A precise mold is fabricated, typically using high-grade steel or aluminum.
- Injection: Molten material is injected into the mold under high pressure, filling it completely.
- Cooling: The injected material is allowed to cool and solidify within the mold.
- Ejection: Once cooled, the mold opens, and the finished product is ejected.
Metal Fabricators: The Role of Injection Molding
Within the realm of metal fabrication, injection molding has a significant role. While traditionally associated with plastics, advancements have led to metal injection molding (MIM), which enables the production of metal parts using similar techniques. This not only enhances the quality and precision of metal parts but also reduces production costs drastically.
Benefits of Metal Injection Molding
Metal injection molding is particularly beneficial for producing small, complex metal components. The process incorporates metal powders with a binding agent, allowing high densities and strong mechanical properties. The key advantages include:
- Complex Shapes: MIM allows for intricate designs that are challenging to achieve with conventional methods.
- Cost-Effective for Mass Production: The ability to produce small parts in bulk lowers overall costs significantly.
- High Tolerances: MIM delivers exceptionally tight tolerances, crucial for precision-engineered applications.
Quality Assurance in Injection Mold Manufacturing
Ensuring quality in the injection molding process is paramount, particularly for businesses in the metal fabrication industry. Manufacturers in China emphasize rigorous testing and quality assurance practices:
- Material Inspection: Raw materials are carefully checked for quality to ensure they meet industry standards.
- Process Monitoring: Throughout the injection molding process, constant monitoring of temperatures and pressures is conducted to maintain quality.
- Final Testing: Finished products undergo final inspections, including dimensional checks and functional tests, prior to shipment.
Challenges in Injection Molding and How to Overcome Them
While injection molding presents numerous advantages, it is not without challenges. Common issues that manufacturers may face include:
- Initial Setup Costs: High initial investments in machinery and mold design can be a barrier. However, this can be mitigated by focusing on long-term savings through mass production.
- Design Limitations: Some designs may pose challenges in terms of mold-making. Collaboration between designers and manufacturers is essential to overcome these limitations.
- Material Constraints: Selecting the right material for the application is critical. Engaging with material experts can aid in making informed decisions.
The Future of Injection Mold Manufacturing in China
The future of injection mold manufacturing in China looks exceedingly promising. As technology continues to evolve, innovations such as 3D printing and automation are integrating with traditional injection molding processes, enhancing efficiency and capabilities.
Integration of Technology
Technological advancements are paving the way for enhanced operational efficiencies, including:
- Automation: Robotics are being increasingly utilized in the injection molding process to reduce labor costs and improve consistency.
- Smart Manufacturing: IoT technologies enable real-time monitoring and data analytics, allowing for proactive decision-making and uninterrupted production flow.
- 3D Printing: Integrating 3D printing with injection molding allows for more complex designs and rapid prototyping, providing a competitive edge.
Conclusion
In conclusion, the versatility and efficiency of injection mold manufacturing in China offer significant advantages for businesses in the metal fabrication industry and beyond. The combination of cost-effectiveness, high quality, and rapid production capabilities makes it an ideal choice for companies looking to excel in today’s highly competitive market.
As manufacturers continue to embrace technological advancements, the future of injection molding in China is set to reach new heights, further solidifying its reputation as a global leader in manufacturing solutions. Companies interested in harnessing these benefits should consider Deep Mould as a trusted partner, ensuring access to the finest injection molding services available.