Understanding High Precision Plastic Injection Molding
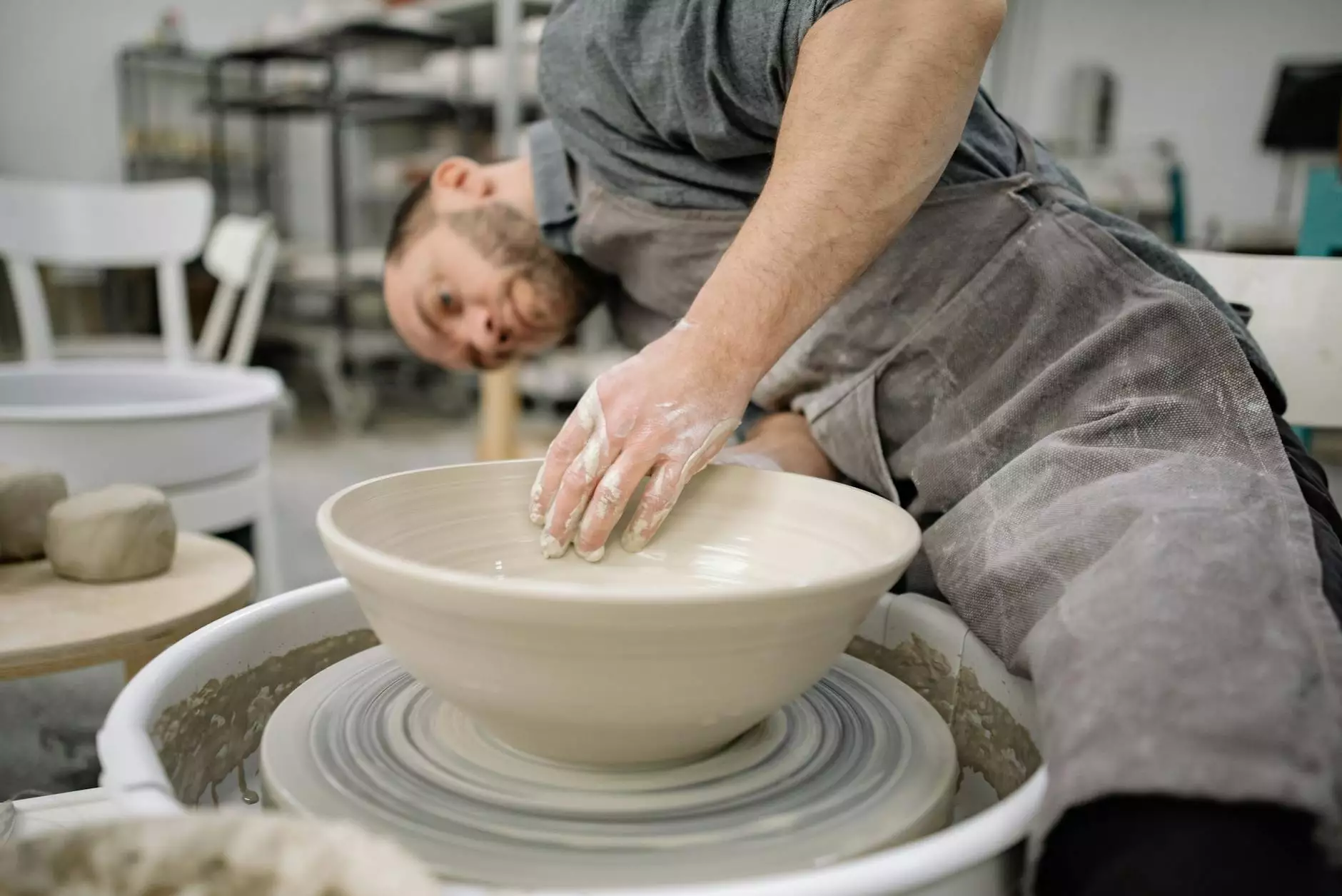
High precision plastic injection molding is a pivotal technology in the manufacturing industry, particularly for businesses that require finely-tuned components made from plastics. This approach enables manufacturers to create parts with exceptional accuracy and minimal waste, leading to significant efficiency in both production and resource management. In this article, we will delve deep into the world of high precision plastic injection molding, exploring its processes, benefits, and relevance, especially in the realm of metal fabricators.
The Basics of Plastic Injection Molding
Plastic injection molding is a method for producing parts by injecting molten plastic into a mold. This process is highly versatile, allowing for the creation of detailed shapes and designs. The stages involved in plastic injection molding include:
- Mold Design: Precision is crucial. Molds must be designed with the right dimensions to ensure consistency in the final products.
- Material Selection: Choosing the appropriate type of plastic based on the desired characteristics of the final product is essential.
- Injection Process: This phase involves heating the plastic until it becomes molten and injecting it into the mold at high pressure.
- Cooling and Solidification: Once injected, the plastic cools and solidifies to form the final part.
- Mold Removal: The finished product is ejected from the mold, ready for inspection and further processing.
Key Advantages of High Precision Plastic Injection Molding
Here are several notable advantages of utilizing high precision plastic injection molding, particularly within the metal fabrication industry:
1. Exceptional Accuracy and Consistency
One of the standout features of high precision plastic injection molding is its ability to deliver parts with incredible accuracy. This consistency is crucial for industries that cannot afford deviations in dimensions, ensuring that every component meets stringent specifications.
2. Cost-Effectiveness
While the initial setup costs for injection molding can be high, the long-term savings make it a cost-effective solution. Once a mold is created, producing multiple parts becomes far less expensive compared to other manufacturing methods.
3. Minimal Waste Production
With advanced designs and high precision, this process results in minimal material waste. Manufacturers can use nearly 100% of the injected plastic, significantly benefitting their bottom line and the environment.
4. High Production Speed
This molding technique allows for the rapid production of parts. High pressure and efficient mold designs enable manufacturers to create thousands of parts in a short period. This speed is particularly advantageous for metal fabricators needing large quantities of components.
Applications of High Precision Plastic Injection Molding
High precision plastic injection molding finds extensive applications across various industries, particularly in sectors where durability and reliability are paramount:
- Aerospace: Components for aircraft and space vehicles demand high precision and reliability.
- Automotive: Parts such as dashboards, bumpers, and other interior components benefit from this technology, ensuring high standards in safety and performance.
- Electronics: From small caps to large housings, precision molding is crucial for circuit boards and electronic devices.
- Medical Devices: The medical industry requires parts that not only meet precision standards but also comply with stringent regulations.
- Consumer Products: Many everyday items, including toys and household appliances, utilize this technology for durability and consistency.
The Role of Metal Fabricators in Precision Molding
Metal fabricators can significantly benefit from integrating high precision plastic injection molding into their processes. By collaborating closely with injection molding specialists, metal fabricators can produce hybrid products that combine metal and plastic effectively. For instance, in creating equipment housing that integrates metal components for strength with plastic for weight reduction and design flexibility, this synergy can enhance overall product functionality.
Collaboration between Plastic Molders and Metal Fabricators
To maximize the advantages of both processes, effective communication and collaboration are essential. Molders and fabricators must:
- Share Expertise: Understanding each field's nuances promotes innovation and efficiency.
- Co-Develop Products: Engaging in concurrent engineering can speed up development times.
- Optimize Designs: Continuous feedback allows both sides to fine-tune designs for better results.
Challenges in High Precision Plastic Injection Molding
Despite its many advantages, high precision plastic injection molding does come with challenges that businesses must navigate:
1. High Initial Costs
As mentioned, the initial costs associated with designing and producing molds can be substantial, though they often pay off over time.
2. Quality Control
Maintaining high standards of quality throughout production is essential. Any discrepancies can lead to non-compliant products, necessitating strict quality assurance measures.
3. Technical Expertise Required
The technology and techniques involved require skilled operators who understand both the machinery and the materials.
Future Prospects of High Precision Plastic Injection Molding
The future of high precision plastic injection molding is promising, characterized by continual advancements in technology and processes. The introduction of innovative materials, such as bio-based plastics and enhancements in mold-making technologies, is set to further improve efficiency and quality.
Moreover, through automation and Industry 4.0 implementations, manufacturers are increasingly capable of monitoring and controlling their processes in real-time, leading to even greater precision and waste reduction.
Conclusion
In conclusion, high precision plastic injection molding stands as a cornerstone technology in modern manufacturing, especially within the metal fabricators sector. Its ability to create high-quality parts with precision and minimal waste makes it an invaluable asset across various industries.
For businesses focused on optimizing production while maintaining quality, investing in high precision plastic injection molding is a strategic move that promises substantial returns. As the industry evolves, those who embrace these advanced manufacturing techniques will undoubtedly find themselves at the forefront of innovation and efficiency.
For more information about high precision plastic injection molding and how it can benefit your organization, visit deepmould.net.